Смесь огнеупорная бетонная теплоизоляционная SL ISOCAST®
Смеси огнеупорные бетонные теплоизоляционные предназначены для получения бетонной теплоизоляционной массы и производства из неё огнеупорных бетонных теплоизоляционных изделий, используемых в виде монолитной футеровки либо в виде конструкционных футеровочных панелей, для ограждения рабочего пространства печного агрегата и для защиты металлического каркаса печи от излишнего перегрева, а также в трубчатых печах риформинга, пиролиза, в печах термообработки металла, в не коррозийной и нейтральной среде, для изготовления огнеупорных бетонных изделий, а также для получения монолитной футеровки в труднодоступных местах без применения вибрации.
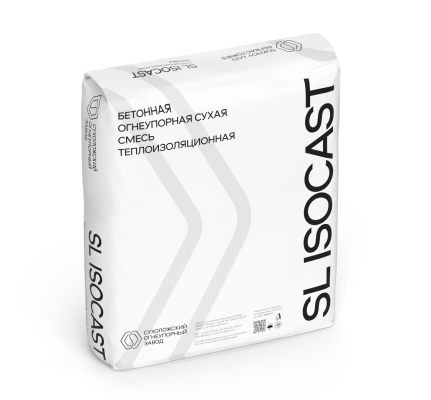
Физико-химические показатели
Наименование показателя |
Значение показателя для марок |
|||||||||||||||||||||||||||||||||||||||||
SL ISOCAST® 0,6-1000 |
SL ISOCAST® 0,7-1100 |
SL ISOCAST® 0,7-1300 |
SL ISOCAST® 105 |
SL ISOCAST® 0,8-1100 SE |
SL ISOCAST® 1,0-1100 |
SL ISOCAST® 124 |
SL ISOCAST® 124 SF |
SL ISOCAST® 1,0-1100 Т |
SL ISOCAST® 1,0-1350 |
SL ISOCAST® 124 Т |
SL ISOCAST® 1,1-1100 |
SL ISOCAST® 1,1-1100 SF |
SL ISOCAST® 1,2-1350 |
SL ISOCAST® 1,2-1350 Т |
SL ISOCAST® 1,3-1300 Т |
SL ISOCAST® 1,3-1350 |
SL ISOCAST® 203 |
SL ISOCAST® 1,3-1450 |
SL ISOCAST® 1,3-1450 Т | SL ISOCAST® 1,4-1800 |
SL ISOCAST® 1,5-1370 SF |
SL ISOCAST® 1,5-1400 Т |
SL ISOCAST® 1,6-1300 |
SL ISOCAST® 1,6-1350* |
SL ISOCAST® 1,6-1400 |
SL ISOCAST® 1,7-1500 |
||||||||||||||||
Массовая доля, %: Al2O3, CaO, Fe2O3 |
34
11
5,3 |
28
21
5,4 |
49 12 0,6 |
28
21
5,3 |
-
-
- |
28
17
4,6 |
29
18
4,3 |
30
19
4,3 |
28
18
4,6 |
47 9 0,75 |
30
17
4,2 |
28
16
4,4 |
29
18
5 |
49
11
0,7 |
45 14 1 |
50
6
0,8 |
49
12
0,7 |
49 12 0,6 |
49 12 0,6 |
52 12 0,6 | 99 0,9 0,05 |
42 11 2,9 |
45 14 2,2 |
55 11 1 |
45 |
65 8 1 |
64 8 1 |
|||||||||||||||
Кажущаяся плотность, г/см3 после сушки при 110 °С после обжига при 815 °С |
0,7
0,6 |
0,9
0,7 |
0,8 0,7 |
0,8
0,7 |
0,8
0,8 |
1,1
1,0 |
1,1
1,0 |
1,1
1,0 |
1,1
1,0 |
1,1 1,0 |
1,1
1,0 |
1,1
1,0 |
1,2
1,1 |
1,3
1,2 |
1,3 1,2 |
1,3
1,2 |
1,4
1,3 |
1,4
1,2 |
1,4
1,2 |
1,4 1,3 | 1,5 1,4 |
1,5
1,4 |
1,5
1,4 |
1,7
1,5 |
1,7 |
1,6
1,4 |
1,8
1,7 |
|||||||||||||||
Предел прочности при сжатии бетона, Н/мм2, после сушки при 110 °С после обжига при 815 °С после обжига при 1300 °С после обжига при 1400 °С после обжига при 1450 °С после обжига при 1500 °С |
1,3
1,4
-
-
-
- |
3,9
3,8
-
- - - |
2,5 1,5 - - - - |
3,7
4,4
-
- - - |
2,1
-
-
- - - |
5,9
5,5
-
- - - |
5,5
4,8
-
- - - |
6,8
6,2
-
- - - |
6,9
5,4
-
- - - |
5,5 3,5 - - - - |
6,2
5,5
-
- - - |
6,2
5,6
-
- - - |
8,7
5
-
- - - |
12
7
-
- - - |
8 5 - - - - |
29
22
-
- - - |
16
9
-
- - - |
11
6 - -
9
- |
11
6 - -
9
- |
13 9 - - - - | 4 2 - - - 13 |
19
19
20
- - - |
16
16
22
20 - - |
29
19
-
- - - |
25 |
17
12
-
- - - |
35
25
- - -
30 |
|||||||||||||||
Остаточные изменения размеров при температуре, % |
0,7 815 °С |
1,3 815 °С |
2 1300 °С |
1,2 815 °С |
- - |
1,3 815 °С |
1,1 815 °С |
0,9 815°С |
0,9 815 °С |
1,4 1300 °С |
1,0 815 °С |
0,8 815 °С |
1,5 при 815 °С 0,8 при 1100 °С |
0,4 при 815 °С 0,9 при 1350 °С |
0,3 при 815 °С 0,9 при 1300 °С |
0,3 815 °С |
0,4 при 815 °С 0,8 при 1350 °С |
0,4 при 815 °С 1,0 при 1450 °С |
0,4 при 815 °С 1,0 при 1450 °С |
0,3 при 815 °С 1 при 1450 °С | 0,1 при 815 °С 0,2 при 1500 °С |
0,2 при 815°С 1 при 1300°С |
0,2 при 815°С 1,5 при 1400°С |
0,2 при 815 °С 1,0 при 1300 °С |
0,1 при 815 °С |
0,2 при 815 °С 1,0 при 1400 °С |
0,1 при 815 °С 0,7 при 1500 °С |
|||||||||||||||
Максимальный размер зёрен, мм |
1 |
6 |
5 |
6 |
- |
6 |
6 |
6 |
6 |
6 |
6 |
6 |
6 |
6 |
6 |
6 |
6 |
6 |
6 |
6 | 2 |
4 |
4 |
6 |
3 |
6 |
6 |
|||||||||||||||
Максимальная температура применения, °С |
1000 |
1100 |
1300 |
1100 |
1100 |
1100 |
1100 |
1100 |
1100 |
1350 |
1100 |
1100 |
1100 |
1350 |
1350 |
1300 |
1350 |
1450 |
1450 |
1450 | 1800 |
1370 |
1400 |
1300 |
1350 |
1400 |
1500 |
|||||||||||||||
Количество воды затворения, % (от количества смеси), в пределах |
90-100 |
70-80 |
58-62 |
70-80 |
** |
40-50 |
40-50 |
36-40 |
38-48 |
40-45 |
38-48 |
32-42 |
36-40 |
30-35 |
35-38 |
20-25 |
20-25 |
30-34 |
30-34 |
30-34 | 6,0-6,3 |
20-22 |
25-27 |
20-30 |
21,7-24,0 |
20-30 |
13-15 |
|||||||||||||||
Коэффициент теплопроводности, Вт/(м⋅К), при температуре 200 °С 400 °С 600 °С 800 °С |
0,093 0,098 0,113 0,118 |
0,120 0,150 0,160 0,180 |
0,158 0,184 0,215 0,269 |
0,120 0,150 0,160 0,180 |
0,180 0,240 0,310 0,430 |
0,140 0,160 0,180 0,190 |
0,140 0,160 0,180 0,190 |
0,140 0,160 0,180 0,190 |
0,140 0,160 0,180 0,190 |
0,202 0,262 0,313 0,355 |
0,140 0,160 0,180 0,190 |
0,190 0,220 0,260 0,280 |
0,190 0,220 0,260 0,280 |
0,222 0,267 0,300 0,355 |
0,220 0,267 0,300 0,355 |
0,200 0,230 0,280 0,300 |
0,260 0,320 0,330 0,360 |
0,230 0,280 0,320 0,370 |
0,230 0,280 0,320 0,370 |
0,295 0,336 0,361 0,418 | 0,741 0,899 0,987 1,090 |
0,319 0,362 0,386 0,412 |
0,334 0,364 0,386 0,400 |
0,340 0,390 0,440 0,570 |
0,376 |
0,340 0,390 0,440 0,570 |
0,557 0,654 0,713 0,830 |
|||||||||||||||
Условный расход смеси на 1 м3, т |
0,6 |
0,7 |
0,7 |
0,7 |
0,8 |
1,0 |
1,0 |
1,0 |
1,0 |
1,0 |
1,0 |
1,1 |
1,1 |
1,2 |
1,2 |
1,2 |
1,3 |
1,3 |
1,3 |
1,3 | 1,4 |
1,4 |
1,4 |
1,6 |
1,6 |
1,6 |
1,7 |
Рекомендуется, чтобы предельная рабочая температура применения, установленная на смесях, была на 100 °С - 150 °С ниже максимальной заданной температуры в чистой, неагрессивной, нейтральной атмосфере теплового агрегата.
*Продукция поставляется по сертификату поставщика
**Смесь марки SL ISOCAST® 0,8-1100 SE состоит из трех компонентов и поставляется в виде сухого компонента и связующего. Количество связующего составляет 65%; общее количество сухого компонента составляет 35%, из них сыпучего компонентна (смеси) 53,5% и волокнистой добавки 46,5%. В сухом компоненте смеси: сыпучем компоненте и волокнистой добавке не допускается наличие посторонних включений. Полное время твердения полученной массы 48 ч. Смешивание сухого компонента и связующего производится непосредственно перед применением.
Обозначения:
T - смесь предназначена для нанесения методом торкретирования
SE - смесь самовспучивающаяся
SF - улучшенная растекаемость
Нормативная документация: СТО 05802307-3-006-2023
Вышеприведённые данные основаны на контроле производственных образцов, являются средними значениями и не могут быть использованы в проектных спецификациях. Данные, представленные на этом сайте, могут изменяться без дополнительного уведомления.
Консультация специалистов
Оформление заказа
Для оформления заказа на поставку продукции вам необходимо
-
На фирменном бланке вашего предприятия оформить заявку, которая должна включать в себя:
- наименование запрашиваемой продукции (либо технические характеристики),
- необходимое количество,
- предполагаемый срок поставки,
- контактные данные.
- При заказе нестандартных изделий (по чертежам) необходимо приложить чертежи запрашиваемой продукции и указать допуска по размерам.
-
Сформированную заявку и чертежи можно направить:
- на электронную почту: tdom@slsoz.ru
- на факс: (34373) 64 3 42; 64 4 63
- или воспользоваться формой обратной связи справа